The Facility Systems Safety program is designed to incorporate system safety into the facility design process as prescribed in Military Standard 882E (Standard Practice System Safety), AR 385-10 (Army Safety Program), DA Pam 385-16 (System Safety Engineering and Management), and new UFC 1-200-01 General Building requirements. The FASS process, also known as prevention through design, is used in the conceptual, planning, design and construction phases of facilities and facility reduction to examine the specifics of the hazards involved, the level of risk, the potential effectiveness of existing codes and standards, and additional design considerations to mitigate hazards. The FASS program is structured to guide designers toward elimination and control of hazards during criteria development and design of facilities. The U.S. Army Engineering and Support Center, Huntsville is the FASS Technical Center of Expertise for the Army.
The FASS process first examines specific hazards involved, level of risk, effectiveness of existing codes and standards, modern technology, and alternate design solutions. Following this discovery and analysis process, the FASS engineer works with the project delivery team to implement solutions to either eliminate or reduce the risk through the use of controls set forth in codes and standards, specially designed controls, or a mix of both control types.
The U.S. Army Corps of Engineers is responsible for the development and implementation of the Facility Systems Safety Program Plan, which details the designer’s plan for executing the systems safety program for a specific project from the concept design phase to the acceptance of the completed facility. The plan describes in detail how each applicable element of FASS is to be implemented. Each Facility SSPP will address the proposed approach to the requirement, the content, and format of the deliverables, and indicate the level of effort for each area. An individually tailored approach based on the contract requirements, the anticipated hazards and the level of risk involved with the specific facility, the SSPP describes how each applicable safety element is to be implemented.
Defining safety and occupational health requirements at the earliest possible time through the FASS process is critical for both the customer and the design/construction team. Identifying issues early can result in cost-savings for the customer, increase customer satisfaction and reduce post-construction project rework/retrofitting to resolve safety issues.
Example 1:
The Army Safety Program lists “dredging” as an initial HIGH-risk project. Great Lakes dredging PDT have included safety into their risk management plan by engaging the Safety Office. When the PDT documented the hazards which were present, they were able to mitigate residual safety risk to the project.
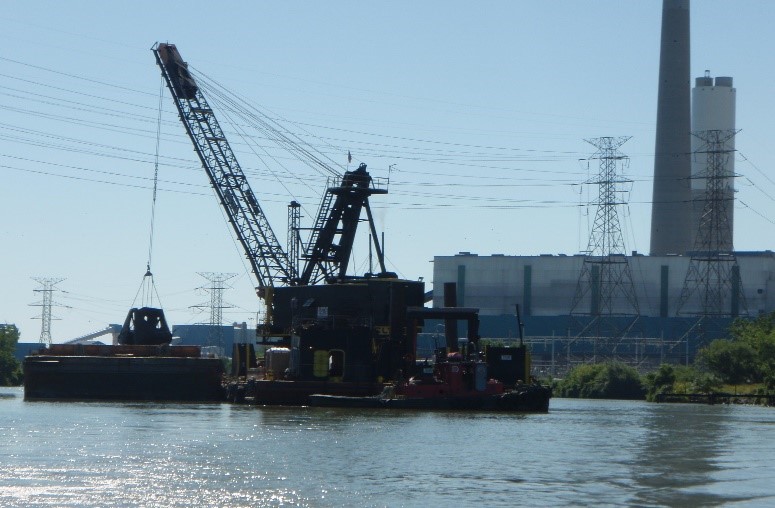
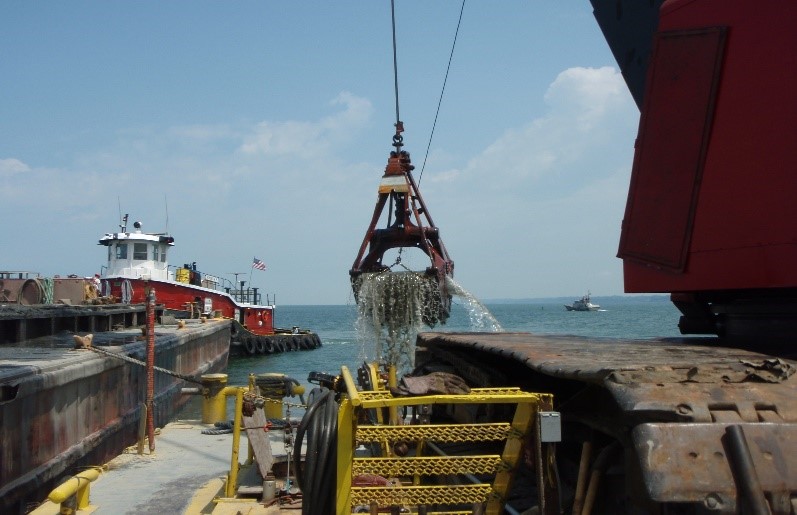
Example 2:
The sunshades on the sides of the Zorinsky Federal Building, a nine-story 432,000-square-foot building, in downtown Omaha, diffuse sunlight, giving the building a 21st-century look and reduced energy costs.
The way the shades accumulated sheets of ice in the winter posed enough risk to pedestrians that the federal government must now spend $200,000 to $500,000 for “ice-mitigation” measures.
If the shades had been designed for ice and installed during construction, the cost would have only been about
$50,000.
Cost savings of $150,000.00 to $450,000.00
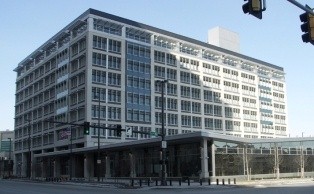
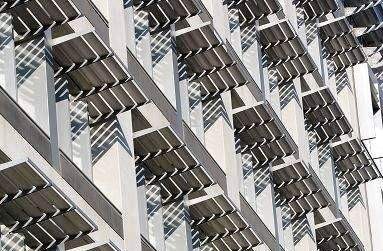
Example 3:
Martin Army Community Hospital at Fort Benning, Georgia. Same issue: If reels had been designed in the conceptual phase and installed during construction, the estimated cost would have been $25,000.
Cost savings of $100,000.00
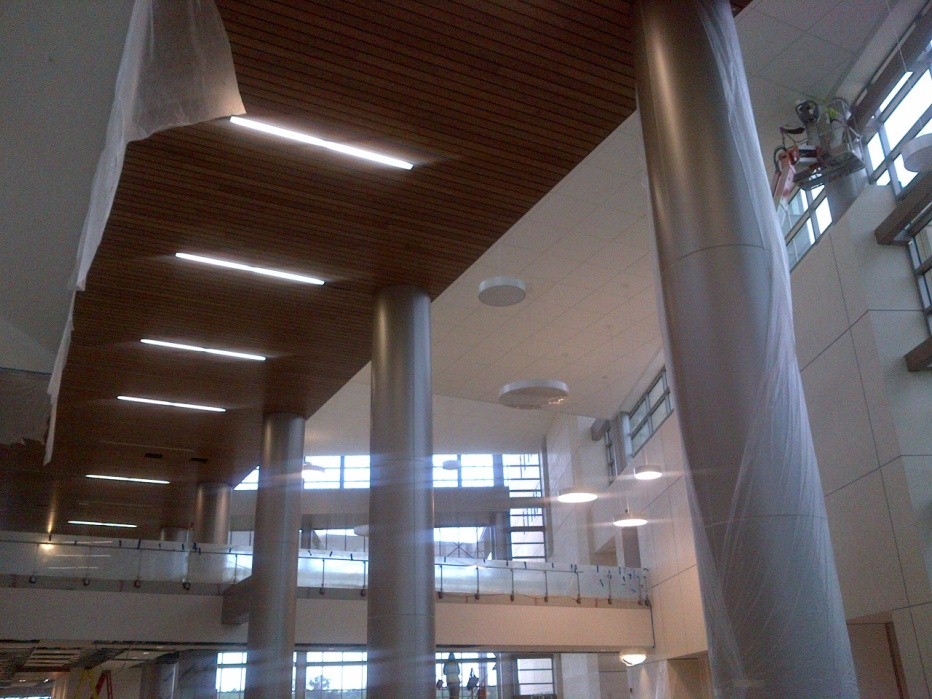
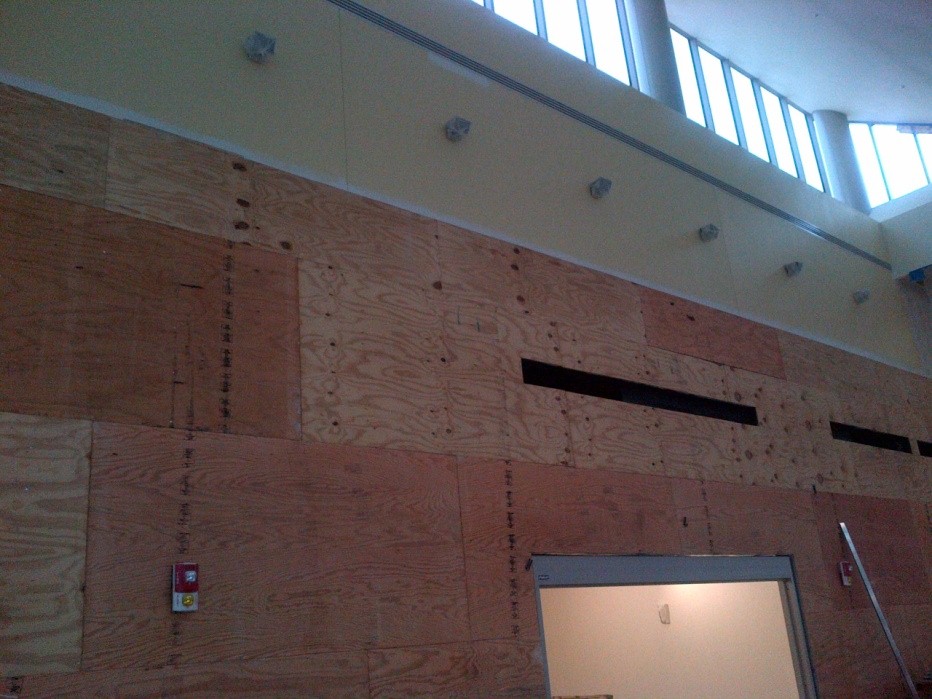
Download the Facility Systems Safety Fact Sheet (PDF) here.